In this blog article, we will focus on the rising problem of counterfeit electronic components in the electronics distribution industry, particularly in North America. We will explore the necessity and structure of Counterfeit Mitigation Programs, the tools and techniques required for counterfeit detection, and the vital role of standards and training in combating this issue.
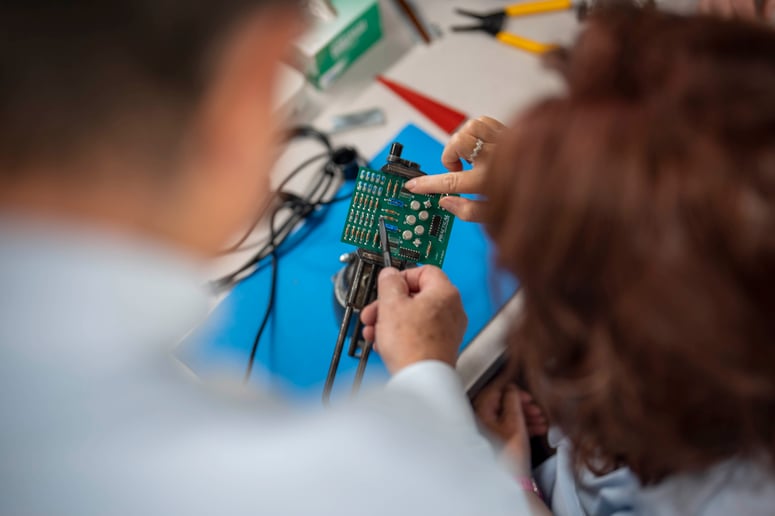
The Escalating Problem of Counterfeit Electronic Components
The infiltration of counterfeit electronic components into the electronics distribution industry poses significant risks, impacting not only the economic stability but also the safety and reliability of products. According to the Semiconductor Industry Association, counterfeit parts cost manufacturers over $7.5 billion annually, translating to nearly 11,000 lost American jobs. The issue has been exacerbated amidst the ongoing semiconductor shortage, which has driven suppliers towards potentially unreliable sources, escalating the risks associated with counterfeit parts further.
Counterfeit electronic components present a myriad of challenges:
- Safety Hazards
They pose serious safety hazards as they may fail to meet the necessary performance or safety standards, leading to catastrophic failures, especially in critical applications like aerospace, medical devices, and automotive systems.
- Financial Losses
The financial repercussions extend beyond the immediate economic loss to manufacturers. It also encompasses the loss of brand reputation, potential legal liabilities, and the costs associated with the replacement of counterfeit components.
- Operational Disruptions
Counterfeit components can cause significant operational disruptions, leading to production downtimes, delays in product delivery, and increased maintenance and repair costs.
The problem is further compounded by the evolution of counterfeiting techniques, making the detection of counterfeit components increasingly challenging. Hence, there's a pressing need for a structured approach to mitigate the risks associated with counterfeit electronic components within the industry.
In the subsequent sections, we will explore the proactive approach of Counterfeit Mitigation Programs, delve into the diverse tools and techniques for counterfeit detection, and emphasize the critical importance of standards and training, spotlighting the EPTAC training program, in fortifying the industry's defenses against counterfeit electronic components.
Counterfeit Mitigation Programs
Counterfeit Mitigation Programs (CMPs) are structured initiatives that aim to curb the infiltration and circulation of counterfeit electronic components within the supply chain, detecting any such components, and managing the associated risks. Here’s a more detailed breakdown of these programs:
- Prevention
- Suppliers and their sub-suppliers are rigorously vetted to ensure they adhere to defined quality standards and have robust counterfeit mitigation procedures in place.
- Staff involved in procurement, inspection, and quality control are trained and certified to recognize counterfeit parts and are updated on the latest counterfeit detection techniques.
- Adhering to industry standards such as IDEA-STD-1010 and IDEA-QMS-9090, which set specific guidelines and quality management system requirements for electronic component distribution.
- Detection
- Conducting thorough visual inspections as per standards like IDEA-STD-1010 to identify any discrepancies that might indicate a part is counterfeit.
- Utilizing advanced testing methods and analytical tools to verify the authenticity and functionality of electronic components.
- Monitoring the market for reports or indications of counterfeit parts and staying updated on counterfeit trends.
- Management
- Maintaining detailed documentation of all procurement, inspection, and testing procedures, and ensuring traceability of all components through the supply chain.
- Establishing protocols for responding to the discovery of counterfeit parts, including notification of stakeholders, quarantine of counterfeit items, and investigation into the source of the counterfeit parts.
- Analyzing incidents of counterfeit infiltration to improve processes, and adopting the latest best practices and technologies for counterfeit mitigation.
- Industry Collaboration
- Collaborating with other stakeholders in the industry to share information on counterfeit threats and best practices for mitigation.
- Participating in industry associations like the Independent Distributors of Electronics Association (IDEA) to stay abreast of the latest developments in counterfeit mitigation and contribute to the development of industry standards.
- Engaging with government and regulatory bodies to advocate for stricter regulations on counterfeit electronic components and to ensure compliance with existing laws and regulations.
- Technology Utilization
- Utilizing state-of-the-art inspection tools and technologies to improve the detection of counterfeit parts.
- Employing blockchain technology to ensure traceability and authenticity of electronic components through the supply chain.
By implementing such counterfeit mitigation programs, organizations in the electronics distribution industry aim to protect themselves and their customers from the financial, legal, and operational risks associated with counterfeit electronic components. This also helps in maintaining the integrity and safety of products, ensuring customer satisfaction, and upholding the industry’s reputation.
Tools and Techniques for Detection
Detecting counterfeit electronic components requires a combination of specialized knowledge, technical skills, and appropriate tools and techniques:
- Visual Inspection
- Check for inconsistent labeling, misspellings, or incorrect logos on the packaging. Examine the component for signs of blacktopping, sanding, or other physical alterations.
- Utilize high-resolution microscopes to inspect the surface quality and markings.
- Employ x-ray inspection to check the internal structure of the component against known genuine parts.
- Perform electrical testing to check the functionality and compare the electrical characteristics of the component with the specifications provided by the original manufacturer.
- Decapsulation involves removing the outer packaging of the component to inspect the die. This can reveal whether the part is genuine or counterfeit based on the die markings and quality.
- Conduct chemical tests to analyze the materials used in the component, and compare them with the materials specified by the original manufacturer.
- Test the solderability of the components to ensure they meet the industry standards and the specifications of the original manufacturer.
- Verify the documentation such as purchase orders, certificates of conformance, and traceability documentation to ensure they are complete, consistent, and originate from reliable sources.
- Ensure that the supply chain is secure and traceable back to the original manufacturer or authorized distributors.
- Employ advanced technologies like scanning electron microscopy (SEM), focused ion beam (FIB) systems, and other high-tech imaging and analysis tools for more detailed inspection and analysis.
- Training
- Training is essential to equip individuals with the knowledge and skills necessary to effectively identify counterfeit components. It provides technical know-how and familiarity with the tools and techniques used in detection.
- The methods counterfeiters use evolve over time, hence training helps individuals stay updated on the latest counterfeit detection techniques and technologies.
- Engaging in certification programs like those provided by organizations such as the Independent Distributors of Electronics Association (IDEA) can ensure that individuals are proficient in the latest counterfeit detection methodologies.
- Collaborate with other stakeholders in the industry to share information on counterfeit threats and engage with industry associations and governmental bodies to stay abreast of the latest developments in counterfeit mitigation.
- Investment in state-of-the-art detection equipment and technologies is crucial to enhance the ability to detect counterfeit components effectively.
Through a combination of training, use of advanced detection technologies, and adherence to established procedures and standards, individuals and organizations can significantly enhance their ability to detect counterfeit electronic components and mitigate the associated risks.
Standards
The IDEA-STD-1010 and IDEA-QMS-9090 standards play a crucial role in counterfeit mitigation programs within the electronics distribution industry. Here’s a detailed look into each standard and their importance in these programs.
IDEA-STD-1010 Standard
The IDEA-STD-1010 standard, titled "Acceptability of Electronic Components Distributed in the Open Market," is spearheaded by the Independent Distributors of Electronics Association (IDEA). It's a pioneering quality standard for visual inspection of electronic components, aiming to aid the electronics component industry in identifying substandard and counterfeit components.
This standard has been referenced in SAE AS5553 and utilized by NASA, emphasizing its importance and adoption in critical sectors. It is based on collaborative efforts by the industry's leading Independent Distributors and has found traction in over 19 countries.
IDEA-QMS-9090 Standard
IDEA-QMS-9090, the Quality Management System Standard for Independent Distributors of Electronics Association Members, sets out specific requirements and practices that independent distributors of electronic components can adopt to meet their customers' requirements. This standard addresses many unique aspects of the Independent Distribution of the Electronics Industry not covered in other Quality Management System (QMS) standards.
This standard aims to combat the challenges posed by substandard electronic components on safety, national security, product performance, and successful commerce. By implementing this standard, stakeholders responsible for purchasing and inspection practices are better educated and coordinated, enhancing the security of the supply chain.
Integration and Application
Both standards are integral to the IDEA’s quality assurance framework, contributing significantly to counterfeit mitigation efforts. The IDEA-QMS-9090 standard, for instance, necessitates certification for all Independent Distributors who are members of IDEA, ensuring that they meet customer requirements effectively.
The standards are not only designed for compliance but are also intended to increase the confidence of all industry stakeholders in the quality of electronic components, assisting with the implementation and maintenance of counterfeit mitigation programs.
Some organizations have incorporated IDEA-STD-1010 entirely into their Quality Management Systems, signifying its importance and effectiveness in counterfeit mitigation. For example, a membership requirement in IDEA is certification to IDEA-QMS-9090, which by extension incorporates IDEA-STD-1010.
These standards represent a comprehensive approach by the IDEA to address the challenges posed by counterfeit and substandard electronic components in the market, highlighting the concerted effort within the industry to maintain high-quality standards and ensure safety and reliability in the electronics supply chain.
Training
Training is an indispensable aspect of counterfeit mitigation within the electronics distribution industry. It equips professionals with the requisite knowledge, skills, and competencies to identify counterfeit electronic components effectively. Here’s a closer look at why training is crucial:
- Counterfeiters are constantly evolving their techniques to bypass detection. Training programs provide professionals with updated knowledge on the latest counterfeit detection techniques and technologies.
- Training ensures a standardized level of proficiency among professionals, ensuring that they are well-versed with the industry standards and best practices in counterfeit detection.
- Practical training provides hands-on experience with the tools and techniques used for counterfeit detection, making professionals adept at identifying counterfeit components in real-world scenarios.
- Obtaining certification from reputable training programs demonstrates a professional's competency in counterfeit detection, thereby enhancing their credibility and the trust that employers and clients place in them.
One notable training program is the Counterfeit Components Workshop offered by EPTAC. This workshop is designed to provide an in-depth understanding of the prevailing counterfeit component issues, inspection techniques, and the standards that govern counterfeit detection. The training encompasses a range of topics including the identification of counterfeit components, understanding of counterfeit component inspection standards, and the implications of counterfeit components on the supply chain.
EPTAC’s training program is particularly beneficial as it not only educates on the theoretical aspects but also provides practical skills essential for counterfeit detection. The hands-on approach ensures that participants are well-equipped to tackle the challenges posed by counterfeit electronic components in their professional endeavors.
Investment in training and continuous learning is a smart strategy for organizations aiming to bolster their counterfeit mitigation efforts. It not only enhances the individual capabilities of professionals but also significantly contributes to the collective competency of the organization in managing the risks associated with counterfeit electronic components.
About EPTAC
EPTAC is an internationally recognized leader in solder training and IPC certification, providing professionals with the skills to accelerate their careers, and businesses, the talent to succeed. For over 35 years, EPTAC has been helping corporations increase quality standards, improve productivity, and maximize profits. With 24 locations in North America, EPTAC continues to expand its offerings and exceptional instructional staff to provide easy access to knowledge and skill-based programs when and where the industry demands it. Access our scheduled programs through our website or schedule your own corporate on-site training. For information, call 800.643.7822 or contact us.